By Frédéric Lert
On the 6th of September 2010, the X3 took off for the first time from the Istres air base in the south of France. 50% aeroplane, 50% helicopter, 100% innovative and successful. The actors of the time remember this extraordinary program…
« CEO Lutz Bertling had decided to launch the study of a fast aircraft,” recalls Daniel Semioli, who was one of the two test flight engineers in the program, along with Dominique Fournier. During a meeting in which I took part, he told us in substance, “The handicap of a conventional helicopter is its speed limited by its rotor. But as this limit is physically impassable, we have to change the concept“.
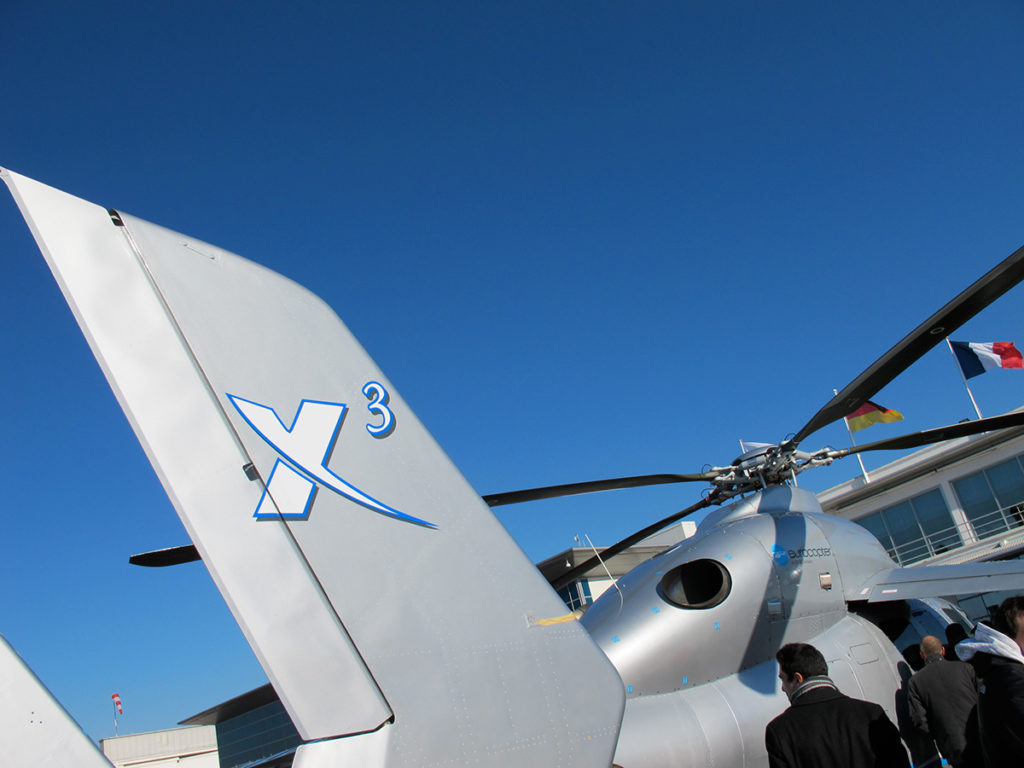
The convertible complexity
The fantasy of the fast helicopter is as old as the helicopter itself. Many avenues have been explored to break the wall of speed related to the physical constraints of the rotor in forward flight. So far, only one hybrid helicopter has been built in the series: the Bell V-22. An aircraft with tilting propellers carried by the Pentagon’s budgets, and reserved for the military because of its complexity, alongside its operating and maintenance costs. But the defects and dangers of the convertible are well known, especially in the transition phase with wingtip flaps that make neither good rotors nor good propellers.
Shadow project
Lutz Bertling’s stated objective is to obtain an aircraft 50% faster than a helicopter, but with simple technical solutions limiting the increase in costs to 20% compared to a conventional aircraft of equivalent size. “Our CEO wanted to launch a small development program that would allow us to respond quickly, and at a lower cost to the question of the feasibility of such an aircraft” continues Daniel Semioli. “The idea did not meet unanimous approval in the company. There was a – moderate – financial risk, of course, but it was above all Eurocopter’s brand image that could be strongly impacted by a failure. The history of hybrid aircraft, with its many accidents, did not argue in our favour ». A very small team, a dozen engineers at most, worked under the leadership of Philippe Roesch (program director) and Thomaz Krysinski to propose a preliminary project to Lutz Bertling. The responsibility of the final decision lands with him, as to whether to continue the project. “Actually this was not about spending a certain amount of money, but about the team proposing to me a minimum budget needed to achieve a flying demonstrator aircraft in a very independent skunk works environment » says Lutz Bertling. « The X3 is certainly one of the achievements in my career I am most proud off ».
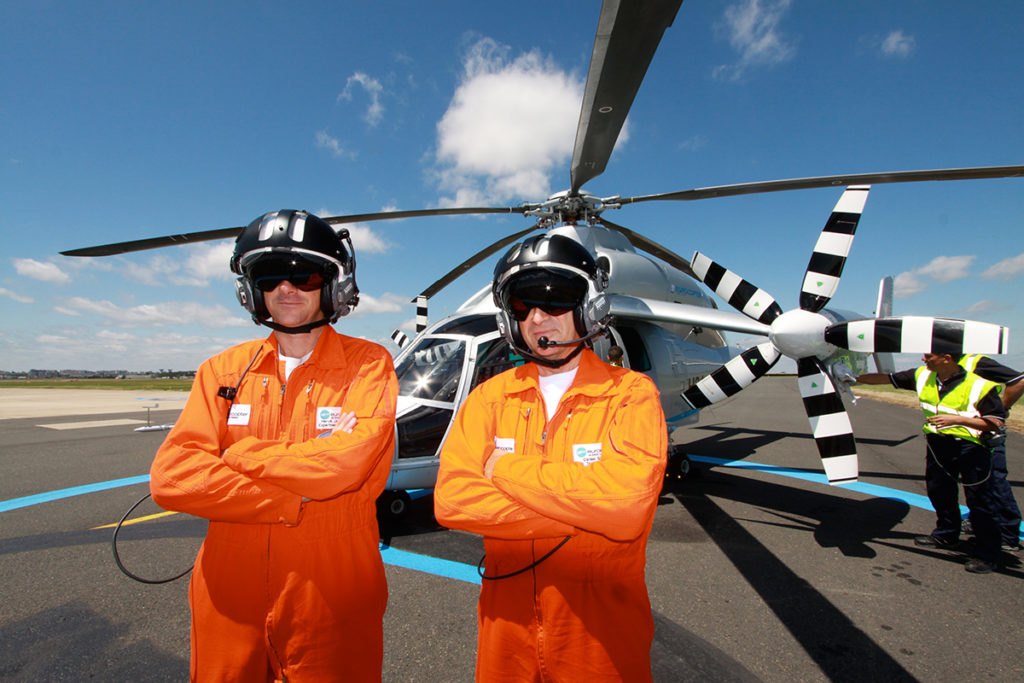
Technology puzzle
In order to move forward quickly and cost-effectively, the design office team makes the greatest possible use of already existing sub-assemblies. The cell is that of an old Dauphin previously transformed to give birth to the EC155 prototype. The rotor is also that of the EC155 prototype. The main gearbox comes from an EC175. It receives two additional lateral outputs for power transmission to the propellers at the wingtips. “The transmission was direct, with no maintenance bearings in the wing” explains Daniel Semioli. “We carried out a lot of tests on the development of the drive shafts, which had to meet the requirements of a super critical shaft“. The manufacturing of the propellers was entrusted to the company MT Propeller, without of course, revealing the very special use that would be made of them. In order to go fast and reduce costs, Eurocopter wanted to use existing propellers with shorter blades and modified twist. The reverse motion of a propeller while hovering in flight, should allow the tail to be balanced. The propeller manufacturer remains perplexed by the requested specifications and explains to his customer ” We don’t know what kind of aircraft you have but it will probably not work very well with the propellers you are asking us for…“. As far as the engines are concerned, the TK team has set its sights on the two RTM322 turbines of the NH90 prototype, whose speed is adapted to the needs of the aircraft being prepared. The rear of the EC155’s airframe is profoundly modified with the addition of a large fixed double tailplane to stabilise the aircraft on the pitch and yaw axis. The wing is fitted with flaps set to compensate for asymmetric rotor wash. A “simplex” type autopilot is slipped under the skin of the aircraft to ensure that everything functions in harmony. “The most extraordinary thing is that the X3 was remarkably stable, and it remained fully controllable throughout the entire flight envelope without the auto-pilot,“explains Hervé Jammayrac, pilot of the demonstrator.
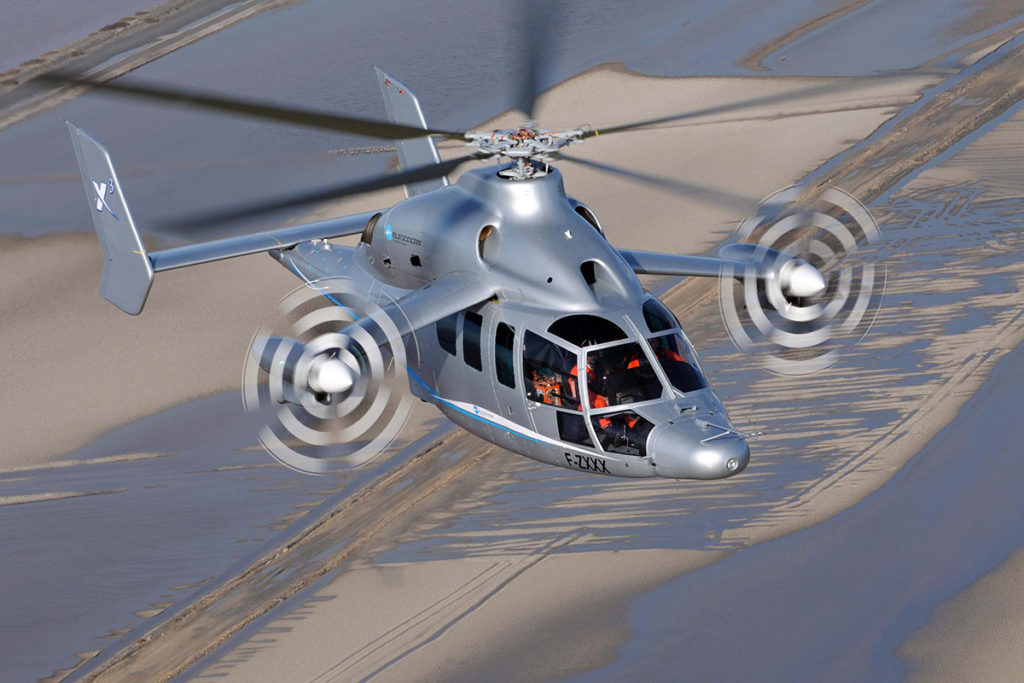
Human adventure
All the assembly work is done in Marignane, in a discreet but very well guarded shed. As the work progresses, new skills are added to the existing team. Specialists are co-opted under the seal of secrecy in each of the company’s sectors. They are chosen on the basis of their technical but also human qualities to guarantee the complete cohesion of the team working in commando mode. For Daniel Semioli as for his colleagues, there is no doubt about it: “We formed a very close-knit group, with the idea that we were on our way to succeed (or fail!) all together! The people chosen were very invested in a project that they knew was unique, and which would mark their professional career and their passage through the company“. At the same time, the future crew discovered the functioning of the aircraft with the help of the SPHERE study simulator, which also enabled Tomasz Krysinski’s team to better define certain parts of the aircraft. “SPHERE was very well done and we were not disorientated when we climbed into the machine for the first flight,” recalls Hervé Jammayrac. “The aerodynamic effects, the gains… we found on the aircraft in flight and everything we had encountered on the ground with the simulator ». On the 31st of July 2010, the prototype left its hangar at dusk. It was towed through the car parks and taxiways of Marseille Provence International Airport to the nearby Etang de Berre. Then it was disassembled into three sub-assemblies, which were placed on a floating barge. It is after midnight when the barge left Marignane and headed to the port of Fos, on the opposite bank. Once there, the sub-assemblies were placed on trucks that only had to travel a few kilometres to reach the Istres air base, in order to cut the trip as short as possible and stay away from busy roads; limiting the arousal curiosity a passage is opened for the sole benefit of the convoy in the fence of the base, in a very isolated sector. At 1pm on August 1st, the aircraft takes possession of its new hangar on the air base. Re-assembly can then begin.
Simplicity of piloting and exceptional performance
« We all shared the same hangar, crew, mechanics, telemetry team, design office, etc. » says a technician on the program. « We had lunch together on site, we thought together, the efficiency was 100%! ». On August 16, 2010 at 6pm, in total discretion, as the base was emptied of its personnel, the X3 carried out its first fixed point in Istres. Three weeks later, on September 6, 2010 at 5pm, the X3 took off for the first time. Two and a half minutes of stationary. « And there’s a major problem: both wings are flapping! The aircraft is at the limit of controllability » recalls Daniel Semioli. The origin of the problem is quickly identified: the flight controls pass through the canopy and the flapping induces parasitic movements, which are amplified by the servocontrols. The solutions were put in place and everything returned to normal within a few days. The rapid succession of flights shows that the X3 combines great ease of piloting with exceptional performance. « Everyday, we were a little more amazed by the potential of the aircraft. The simplicity of the technical solutions, which was one of the major characteristics of the aircraft; our choice to play with the rotor speed and propeller pitch, without ever losing efficiency; all of these aspects surprised the aeronautical world, which sometimes thought that this level of simplicity would not work, » Daniel Semioli sums up. « A helicopter pilot will master the piloting of this aircraft in less than five minutes. Contrary to what is known with convertible aircraft, the vertical and horizontal flight phases follow one another without transition, without ever endangering the aircraft’s occupants ».
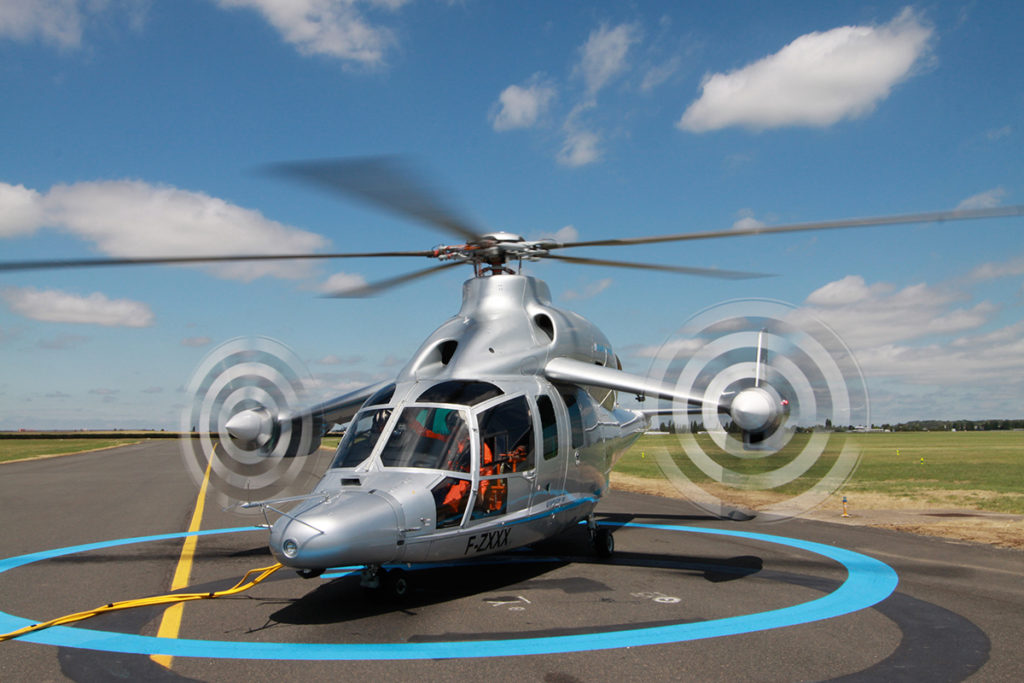
At the beginning of 2013, with the entire flight envelope open, the X3 unofficially breaks the speed record for a gyrodine, at 255 knots. The aircraft then accumulated just over 140 hours of flight time, well over the 100 hours initially planned. But the success is such that the aircraft is used in a large number of communication operations, including an exceptional “demo tour” in the United States. All the objectives of the technological demonstrator have been met and, as a sign of its success, the program is accumulating honours: Howard Hughes trophy, Hall of Fame for innovation in the United States, Gold Medal of the French Aeroclub. Now it’s time for the Racer, which promises to revolutionise vertical flight.